Estate sales are a popular way to dispose of items and raise money. Many families hire professional estate sale companies to help with the process. These companies handle preparation tasks such as sorting and organizing items, advertising to drive traffic, and overseeing the event.
They also provide appraisals for determining item value and assisting with pricing strategies. They may use online listings and local advertisements to promote the sale. For more information, click Learn More Here.
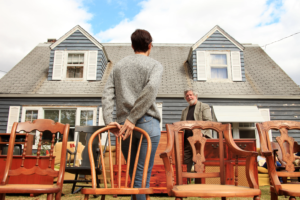
Estate sales are a popular way to liquidate personal belongings when facing major life changes such as moving, downsizing or settling an estate after the death of a loved one. However, the process is often complicated and requires a professional to execute it successfully. Estate sale companies are a crucial partner in this endeavor, taking on the complex tasks of assessing and appraising items, organizing and displaying them for the public to see, pricing the goods based on market value and advertising to attract potential customers. They also oversee the day-of-sale activities and may even handle donating or disposing of unsold merchandise.
Because of these responsibilities, estate sale companies typically charge between 30% and 50% of the total sale revenue. When choosing a company, it is important to research their performance and customer feedback. You can also visit a sale they are holding to get an idea of their expertise.
Some people assume that estate sales are overpriced, but this is not always the case. Most estate sales are conducted by professionals who are experienced in assessing and pricing items based on their condition, age and demand. This ensures that customers are not overpaying for an item and provides opportunities for negotiation. Additionally, many estate sales are open to the public, making them a great place to find bargains.
While estate sales are often a result of unfortunate events, they can also happen for positive reasons such as downsizing for retirement or moving to a new location. Regardless of the motivation, estate sales offer a unique opportunity to explore a variety of personal collections and discover valuable treasures.
Unlike garage sales, estate sales are usually conducted in the home of the seller or family members and feature a more extensive selection of household items and collectibles. They can be held in a private or public setting and are generally held on a weekend. The proceeds from these sales can be used for a variety of purposes, including paying debts or settling an estate. Disputes over the value of estate assets and how they should be distributed can occur between family members, creditors, and financial institutions. These disputes can lead to litigation and the need for an estate liquidator.
They are a way to dispose of belongings
Estate sales are a unique way for individuals to dispose of belongings that they no longer need, often after experiencing a significant life event. They are different from garage sales in that they typically sell everything inside a home and often offer higher-value items like antiques or rare pieces of art. The sales are usually held over a weekend and are organized by professional companies that handle the process of appraising, organizing, and displaying items for sale. These companies also oversee the day-of-sale activities, ensuring that everything runs smoothly and efficiently.
Estate sales can be a great way to generate income, and the profits can be used to pay bills, pay for an upcoming vacation, or save for future expenses. Additionally, the process of sorting through and selling unwanted belongings can be therapeutic, allowing individuals to gain perspective on what is really important in their lives. Estate sales can also be a good way to honor deceased family members by giving their possessions a second life, rather than letting them sit in storage or collecting dust in the attic.
Buyers can expect to find a wide range of items at estate sales, including everyday household goods, furniture, and electronics. Shoppers may also find unique curiosities, such as memorabilia or collectibles. These items can be a fascinating window into history and a glimpse into the interests of the deceased. They can also be a great opportunity for shoppers to find treasures that they may not have found in retail stores.
While shopping at an estate sale, shoppers should be aware of the potential risks. These sales attract a large number of people and can pose security risks. In addition, a sale may have legal and tax implications that require careful consideration. Additionally, a large number of items may be stored on site and can be subject to theft or damage.
To avoid these risks, sellers should consider hiring an experienced professional to manage the estate sale. This will help to ensure that the event is executed effectively and securely, while maximizing revenue for the estate. The company can also help with other aspects of the process, such as advertising and ensuring that items are priced accurately.
They are a way to raise money
Estate sales are a great way to get rid of unwanted items and raise money. The proceeds from these sales are often used to pay debts, cover living expenses or invest for future use by the family. However, it is important to plan carefully before starting an estate sale. This will ensure that the process is executed efficiently and smoothly, resulting in an optimal outcome for all parties.
Estate Sales are similar to garage sales but offer a wide variety of merchandise, from clothing and furniture to antiques and collectibles. They are also typically much more organized and require a professional management team. They are usually held after a major life event, such as a death or divorce.
An estate sale is a great way to find unique items at a fraction of their original cost. However, it is important to be aware of the etiquette involved in attending an estate sale as well as how it differs from a normal retail store. For example, you should always arrive early to avoid crowds and line up behind a number sheet before entering the home. This is to prevent people from getting ahead of others, and to help everyone have a fair chance to look at everything before the sale begins.
Most estate sales are limited to a specific amount of people at any given time. They also may have a sign-up sheet, or they might give out numbers beginning at a specified time. In either case, it is good estate-sale etiquette to stick with your number until you leave the house. If you do not follow this rule, you might miss out on a valuable piece of merchandise.
Another important tip is to be respectful of the homeowners. Many of them are grieving during the estate sale, so it is important to remember this while shopping. If you are rude or aggressive, you could offend the family members who have been left behind.
The sale organizers should clearly label each item with its price and description. They should also advertise the sale online and in local newspapers. This will help attract a larger audience and ensure that the sale is successful.
They are a way to get rid of clutter
Estate sales are an excellent way to get rid of clutter and clear out your home. Whether you’re moving, downsizing, or simply want to simplify your living space, this process can help you make room for the things that matter most in your life. Unlike yard sales or thrift stores, which are often run by volunteers, estate sales are typically managed by professional companies that specialize in organizing large collections of objects. They can help you sell off your valuables and make the process of clearing out a home much easier.
The estate sale begins with an evaluation of the items that will be sold and their relative value. Once the items have been chosen, they are arranged in rooms and set up to attract buyers. It’s important to carefully sort and label the items to avoid any confusion or miscommunication with customers. This will help buyers find exactly what they’re looking for, and it’ll also prevent them from buying items that aren’t in their price range.
Typically, estate sales last for a few days or a week and are open to the public. The items for sale can include jewelry, furniture, artwork, crockery, power tools, and other household goods. They may be organized by the executor of an estate or by a probate court.
When you attend an estate sale, it’s a good idea to bring cash. Most estate sale companies do not accept credit cards, so it’s important to plan ahead and bring enough cash to cover your purchases. Also, be aware that the prices at estate sales are usually higher than those of other retail outlets. If you don’t feel comfortable spending a lot of money, it’s best to walk away. Lastly, be sure to wear comfortable shoes and have bags or boxes in your car to transport your items. This will prevent you from getting a sore back while carrying your treasures home.